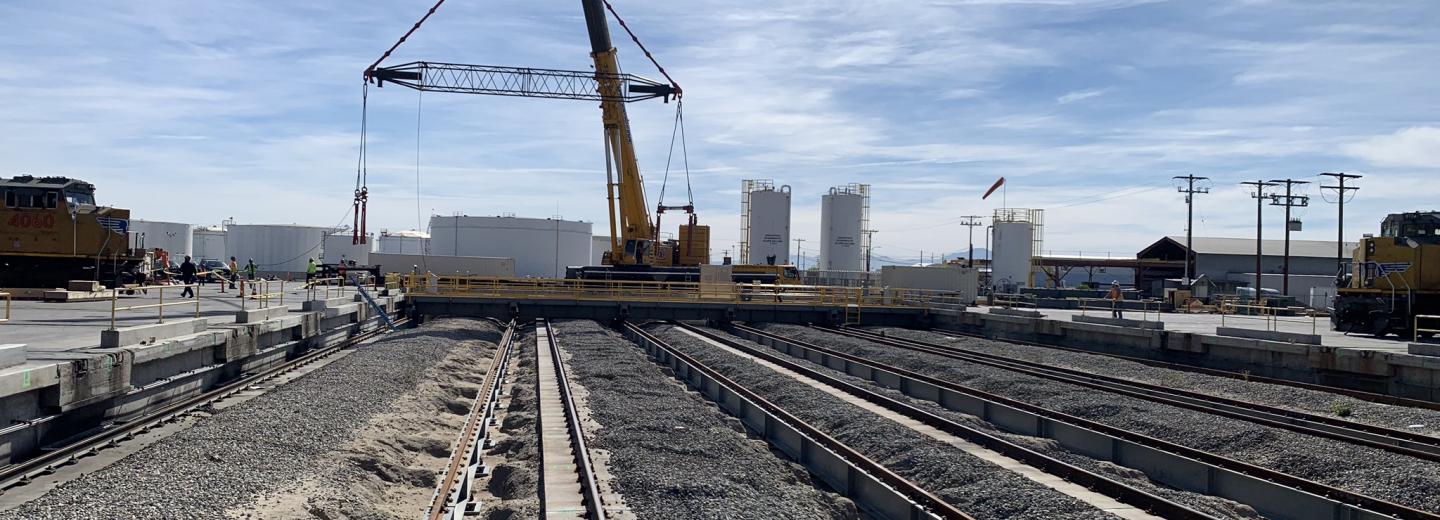
Granite’s Union Pacific Railroad West Colton Yard Transfer Table Project Receives Associated General Contractors of California 2020 Constructor Award
In late January 2021, the Associated General Contractors (AGC) of California awarded Granite the 2020 Constructor Award for specialty Contractor Under $10M for the Union Pacific Railroad West Colton Yard Transfer Table project – one of two AGC of California awards Granite has received this year.
Union Pacific Railroad’s (UPRR) owned and operated mechanical diesel maintenance facility in Colton, California operates 24/7 and after 12 years of operation, the infrastructure was beginning to fail and impact operations. The $6.6 million West Colton Yard Transfer Table Replacement project included the removal and replacement of the deteriorating foundation and a transfer table used to transfer locomotives from the track to the maintenance bay for service and repair.
Since the facility continued to operate during construction, continuous communication between the Granite team, train crews, and subcontractors was essential to plan the safe execution of the project. Coordination began with the use of work plans that were reviewed and discussed at two daily meetings, an essential component of every safety plan. Before delivery, Granite created specialized work plans that included the critical pick plan for unloading the new transfer table and an hour by hour schedule of each day’s installation materials, and equipment and material placement logistics. These work plans also outlined how power would be switched over to the new bus bar system allowing for both transfer tables to run in the pit during the installation of the outside foundation piles and beams.
Granite performed the removal of the existing spread footing concrete foundations and replaced them foundations with 150 20-inch diameter driven pipe piles at a refusal depth of approximately 60-feet. Granite installed pile plates and 48 21-inch by 132-inch steel foundation beams, 1470-linear feet of 135-pound rail mounted to the foundation beams utilizing welded rail clips. Granite built a new 99-foot by a 17.5-foot structural steel bridge that utilized Demag crane wheels, SEW Drive motors, Sumitomo gear reducers, and state of the art control systems. The new transfer table met all required American Railway Engineering and Maintenance-of-Way Association bridge specifications.
This transfer table was the first one of its kind in the Union Pacific System and required a management team well versed in structural steel, and the movement of mechanical components and electrical systems. To expedite the schedule, Granite led constructability reviews and collaborated with the project designer to finalize design and vet construction solutions and innovations. The project team took a phased approach to the construction of the deep pipe file foundations by starting work on the center beams that were offset from the original spread footing foundations allowing fabrication of the table at an offsite facility to occur simultaneously without any interruptions to the facility’s operations.
“One unique challenge of this project was the inability to make major adjustments to the transfer table once it was placed in the pit. Our team built a mockup test pad that simulated the final configuration in the pit and allowed us to run all appropriate system checks offsite in a safe uncongested work environment,” said Granite Construction Manager Muin Mustafa. “The ingenuity of the team helped us tackle an added challenge when the manufacturer's catalog of drive shafts did not match the custom configuration. The team quickly pivoted to collaborate with the design team to create custom shafts that did not hinder the project schedule nor impact the budget.”
The fabrication facility, located in El Centro, California, did not have a controlled weather atmosphere large enough to fabricate the table indoors so the table was fabricated outdoors in very hot temperatures affecting the very stringent tolerances of 1/32 degrees or 0.0007 inches of parallel offset for the axle alignment and mechanical components requirements and +/- 1/16 inches of alignment for the structure components requirement. Granite used faro laser technology to monitor the movement of the steel members and based on the data collected, performed the bolt up of the structure at night which ultimately allowed for final machining and achievement of the stringent tolerances.
The new transfer table measured 99-feet long, 17.5-feet wide x 8.5-feet tall, and weighed 225,000 pounds, the contract called for delivery in two pieces. Granite quickly recognized that two deliveries on UPRR’s operations would interrupt the train operations for extended periods. To mitigate this, Granite suggested utilizing specialized lifting equipment to maintain structural steel alignments without stressing the members during critical loading and unloading lifts. This plan also included specialized trailers with independently operated, remote-controlled steering wheels able to withstand the full weight of the table from the fabricator’s facility to its final destination in one single piece. These innovations saved the project time four weeks of assembly on the job site and allowed the mechanical facility to operate without extended interruptions.
Through complete cost and schedule transparency, excellent communication, and collaboration amongst the Granite team, UPRR, and its designers, the teams worked towards the common goal to maintain the project budget without jeopardizing the design nor function of the table's intended use. Changes to project plans and involved cost changes were handled professionally at the lowest levels and cost savings alternatives were welcomed. The teams prevailed and the project was completed on time and budget, and no OSHA recordable injuries, environmental citations, or claims.
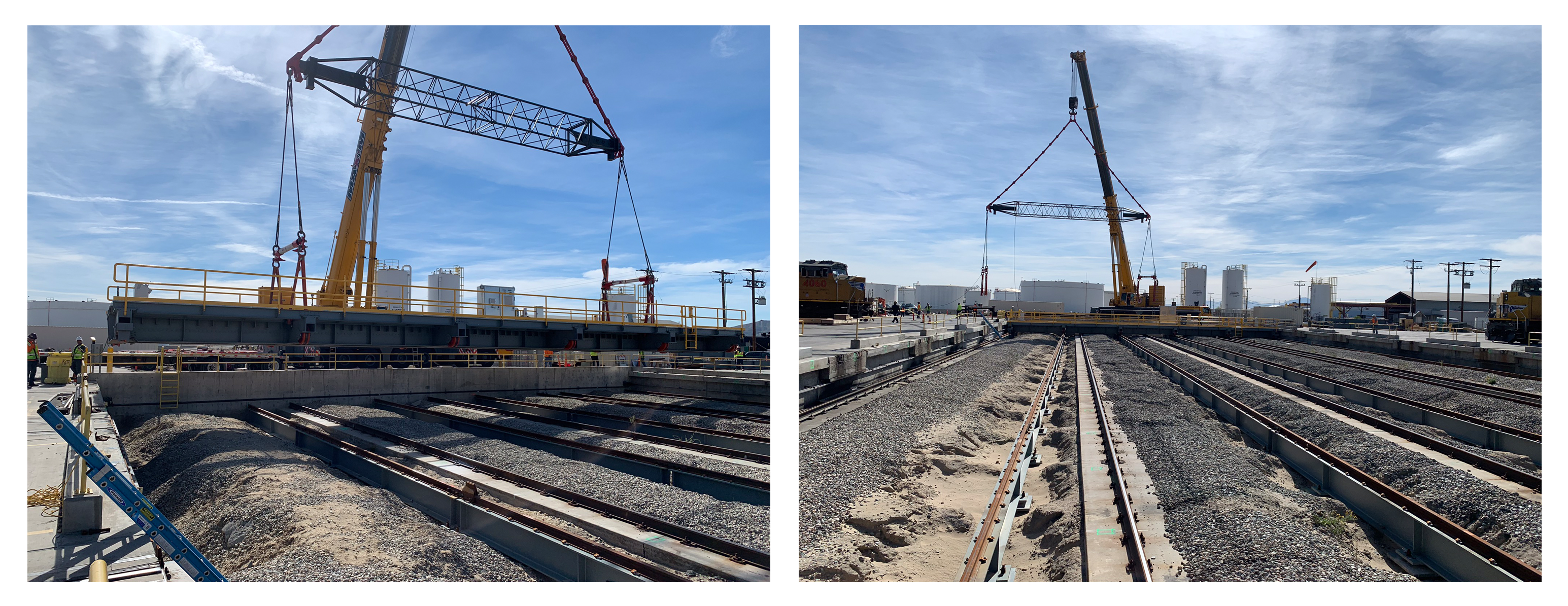